Giving the Collection a Lift: Uncovering the Design History of the World Trade Center’s Elevators
Giving the Collection a Lift: Uncovering the Design History of the World Trade Center’s Elevators
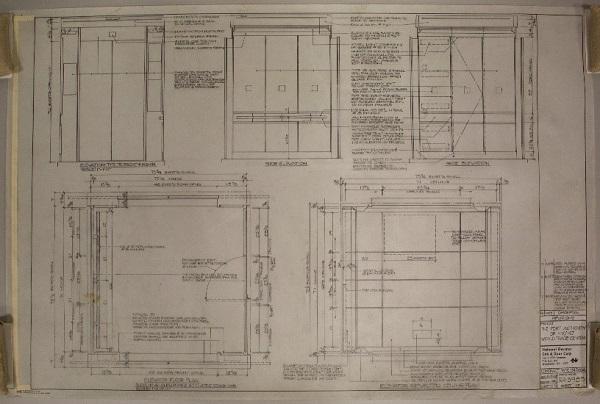
From the outset, elevators functioned as the vital circulatory system of the World Trade Center and played a significant role in the efficient functioning of these quarter-mile high workplaces. Recently, the 9/11 Museum acquired two gifts that highlight the off-stage care that went into their design: an archive of materials related to the redesign of the WTC elevator cabs beginning in the early 1990s, and the donation of the iconic elevator call-button panels that served many of the elevator banks.
The first of these gifts comes by way of the National Elevator Cab and Door Corporation, a family-run business that began producing and installing elevator cabs in 1929. In 1991, the company was hired by the Port Authority of New York and New Jersey to remodel nearly 200 elevator cabs in World Trade Center Buildings 1, 2, 3, 4 and 5, along with those servicing the Vista Hotel (WTC3). Earning the contract was a huge achievement for this local company.
This punch press machine at National Elevator Cab and Door Corporation dates from 1981. It was one of the first of its kind in the United States, and was at long last retired and replaced with a newer machine this fall.
National is a full-service business and undertook all the work for the large WTC job itself, from producing designs and manufacturing the required materials to installing their products within the existing elevator shells. Harold Friedman, the company’s chairman for 50 years, considers an elevator cab to be a 5-by-6-foot room in which every detail is viewed up close by the room’s occupants; therefore, no part of the design or product could be overlooked.
By 1993, the design scheme for the WTC’s elevators had been established. It featured porcelain enamel panels with aluminum-painted divider strips, handrails resting on marble chair-rails, painted aluminum ceilings and a mirror-finished stainless-steel light cove. The wall panels would be outfitted with attached clips so they could be easily inserted into a template that then screwed onto the elevator shell wall. This made the panel installation process as efficient as possible and easily removable for the next elevator remodel. Remodels were typically undertaken once every 20 years.
National Elevator Cab and Door Corporation’s drawing no. RR-3985 showing elevator side elevations, floor plan, and ceiling plan. Hand-drawn by engineer Mike Modinia, March 11, 1993.
When a truck bomb was detonated below the North Tower at 12:18 p.m. on Feb. 26, 1993, some personnel working for National were in the process of transferring materials stationed in the B2 level of the WTC’s underground garage up to the 61st floor. Fortunately, they were unharmed by the explosion that killed six individuals — each of whom was either on the B2 level or passing through the building’s nearby parking garage. The damage produced by the terrorist bomb caused lengthy delays to the elevator renovation project, halting all work for eight months.
A National employee inserts a large piece of sheet metal into a press brake to bend it into a specified shape.
National finally finished this monumental job in 1999. “It was a tough trip, to say the least,” said Friedman. Afterward, Friedman received a letter of commendation from Alan Reiss, director of the World Trade Center, who reflected:
“We understand that contractors, when working at the World Trade Center, encounter many challenges. Certainly, this contract represent[s] a few more than usual. I am happy to say that they were met very professionally and with the spirit of cooperation.”
The Museum has recently processed a multi-part gift from the National Elevator Cab and Door Corporation which encompasses their hand-drawn elevator design drawings from 1993, one of 193 original handrails manufactured for this project, a porcelain enamel material evaluation and the 1999 letter sent by Reiss. Also included are original elevator drawings from the Otis Elevator Company dating back to the WTC’s 1968 construction. These were given to National in 1993 as part of a job informational package prepared by the Port Authority.
WTC elevator call button assembly. Stainless steel. Manufactured by Elevator Products Corp, Little Falls, N.J., 1993.
The second gift, an elevator call button panel designed for one of the Twin Towers’ sky lobbies, was transferred to the Museum by Bob DiChiara, who had had served as an assistant director of the World Trade Department under the Port Authority. This object was probably manufactured for renovations within the Towers after the damage caused by the 1993 garage bombing attack. This one was never installed. The design of the push plate bears stylized images of the tridents which formed Minoru Yamasaki’s signature arched element in his architectural scheme for the Twin Towers, also illustrating the attention invested in every detail of this elevator system.
By Jasmine Shevell, Preparator/Conservation Technician, 9/11 Memorial Museum
Previous Post
Remembering Keithroy Marcellus Maynard, Devoted Father and Vulcan Society Member
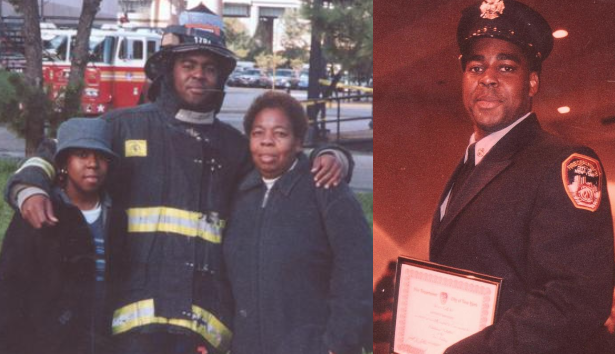
Born on the small Caribbean island of Montserrat, Keithroy Marcellus Maynard moved to New York City when he was 13.
Next Post
The Lens: Capturing Life and Events at the 9/11 Memorial and Museum
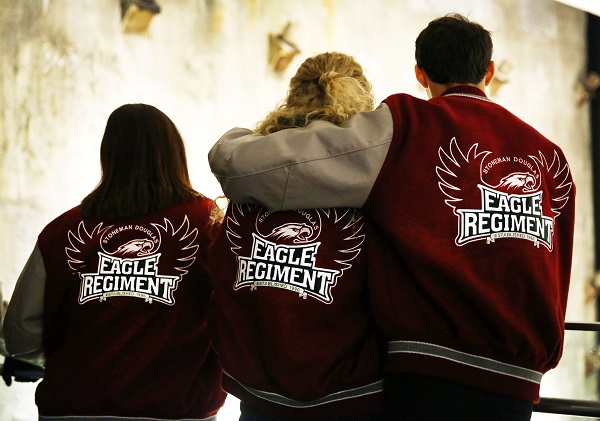
A group of 55 students from Marjory Stoneman Douglas High School, the school in Parkland, Fla., where 17 people were killed by a gunman on Feb. 14, 2018, visited the 9/11 Memorial & Museum yesterday morning.